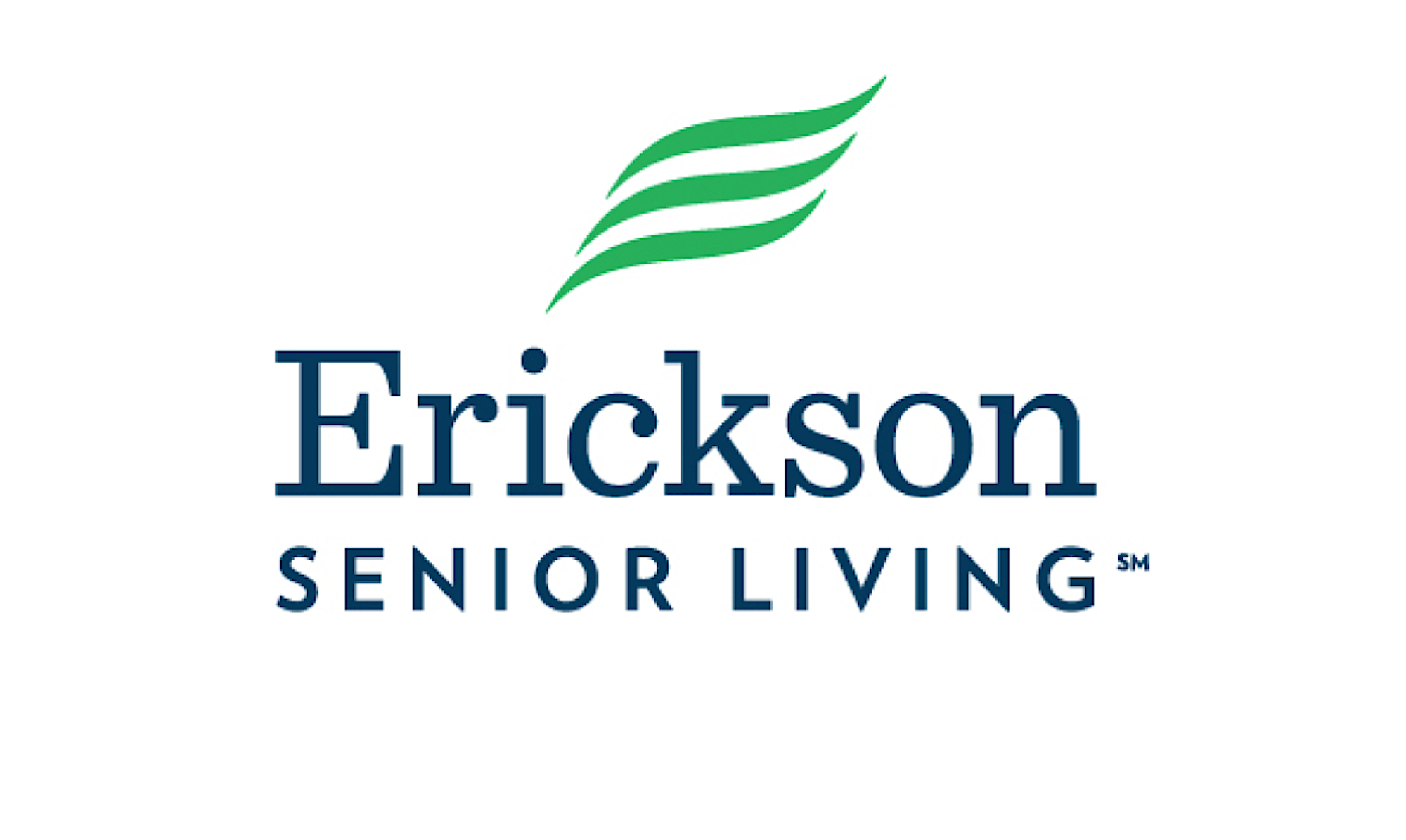
Mission Statement
Founded in 1990, C & C Construction Management Inc. strives to continually raise the bar in the quality and services we provide.
We have built our reputation based on a philosophy of high morals and loyalty to our clients.
Our goal is to build lasting relationships with our clients achieved through satisfying their objectives through quality workmanship and projects completed on time and within budget.
We strive to be resourceful, creative and solution-oriented giving us the ability to offer new and innovative approaches to all problem solving.
Company Information
C & C Construction Management, Inc.
10063 Sandmeyer Lane
Philadelphia, PA 19116
(215) 673-1799
www.cccmgmt.com
Contact:
Vincent P. Celenza- President & CEO
Vcelenza @cccmgm.com
Frank Stoltz – Director of Project Development
FStoltz@cccmgmt.com
Officers:
Vincent P. Celenza – President & CEO
Gina Tracy – Treasury
We are a subchapter S corporation, incorporated under the laws of Pennsylvania.
C&C’s Safety Record:
Experience Modification Factor is 0.8950.
We have a sound financial base which include banking relationships with:
Santander Bank (formerly Sovereign), Citizens Bank, First Trust, TD Bank, and Provident Bank of New Jersey
Surety Company:
Ohio Casualty Company
Agent: Rosenberg & Parker
455 S. Gulph Road, Suite 400, King of Prussia, PA 19406
Contact: Christine Hrusovsky (610) 667-5200
Heartis. Senior Living – Warminster, PA
Daniel Marsicano
Senior Construction Associate
(972) 274-3223
DMarsicano@caddis.com
Gary Puma
CEO Springpoint Senior Living at time of construction
(609) 987-3976
garytpuma@gmail.com
Bonding Capacity Letter
Accident Prevention Program:
Safety is president/CEO Vincent P. Celenza and C &C Construction Management Inc. (CCCMI) top priority. Initially everyone involved in the project must attend and sign affidavits that they were present at our kick off safety meeting. As the project develops we establish a “safe culture” on the site where subcontractors are asked to watch over each other, if they see a potential risk they must alert the responsible parties and our on site field team before their work can commence.
Our team works continually to maintain a safe working environment. Our safety officer, Gary Grisafi visits every site throughout the project to oversee that our field staff is in compliance with OSHA requirements, documentation and establish that every team member and subcontractor has received the proper training, PPE, fall protection, toolbox talks and to reiterate site-specific hazards and safe work practices.
Quality Control
C & C’s quality management system includes comprehensive operating procedures, checklists, and proper employee training to ensure an outstanding final product. Our quality assurance officers meet with onsite superintendents regularly to ensure that company expectations are met throughout all stages of construction, rough, prior to sheetrock, closing up ceilings, all finishes etc. We utilize 360 cameras that are integrated with our Procore platform to identify flaws that need correction. The QC team sends an alert via procore to the responsible subcontractor so there is no confusion, once the item is corrected the QC team does a final walk through. We’ve found that this QC phase minimize any architect/owners punch list.
Throughout the project our in house project coordinator gathers all necessary product information, Flame Spread Data, warrantees, cleaning instruction, MSDS, as builts, etc for when the building is complete a digital copy of all close out documentation is ready when the building is occupied. Our team members and our subcontractors understand our commitment to quality and never accept “good enough.” Our stringent quality control results in expedited turnover to the owner.
Green Construction Experience
The C&C project team has been engaged in many projects involving sustainable features and energy efficient design including Green Enterprise, Energy Star, LEED, and Green Futures. We continually strive to keep abreast of current sustainability trends through seminars, training, and on-line courses.
One of our completed projects, Robert Noble Manor, was constructed utilizing many Green Elements. This project complied with the requirements of the Green Futures program and was built using the modular construction approach, which further enhanced the sustainability of the project. C&C worked closely with the design team assisting in the selection of materials, means, methods, and equipment to exceed the sustainability goals while maintaining the budget. Some of the items featured on this project are Low VOC products, Non-vinyl flooring, Energy Star appliances, high MERV air filters, low flow plumbing fixtures, energy efficient lighting, and an in-house recycling center with a program for each resident unit. Upon completion of the project, 3rd Party Green Future Certified Engineers commissioned the building and performed the required field testing such as blower door tests to ensure the facility performed per the stated design requirements
In addition to completing projects with Green Elements, C&C has implemented strategies to support sustainable practices such as a company-wide recycling program at our offices and on our job sites by utilizing comingled or single stream dumpsters to divert waste from landfills. We have also renovated our offices to incorporate LED lights, Energy Star appliances, and low flow plumbing fixtures.
C&C utilizes local suppliers and manufacturers whenever possible to not only reduce the carbon footprint of materials used on our projects, but to also support the local economies. A few examples are utilizing local Millwork Vendors, purchasing flooring from Floorfolio, who manufacturers their products in New Jersey, and working with lighting consultants to use light fixtures manufactured in New Jersey, Massachusetts, and other areas in the United States.
Green Construction Experience
The C&C project team has been engaged in many projects involving sustainable features and energy efficient design including Green Enterprise, Energy Star, LEED, and Green Futures. We continually strive to keep abreast of current sustainability trends through seminars, training, and on-line courses.
One of our completed projects, Robert Noble Manor, was constructed utilizing many Green Elements. This project complied with the requirements of the Green Futures program and was built using the modular construction approach, which further enhanced the sustainability of the project. C&C worked closely with the design team assisting in the selection of materials, means, methods, and equipment to exceed the sustainability goals while maintaining the budget. Some of the items featured on this project are Low VOC products, Non-vinyl flooring, Energy Star appliances, high MERV air filters, low flow plumbing fixtures, energy efficient lighting, and an in-house recycling center with a program for each resident unit. Upon completion of the project, 3rd Party Green Future Certified Engineers commissioned the building and performed the required field testing such as blower door tests to ensure the facility performed per the stated design requirements
In addition to completing projects with Green Elements, C&C has implemented strategies to support sustainable practices such as a company-wide recycling program at our offices and on our job sites by utilizing comingled or single stream dumpsters to divert waste from landfills. We have also renovated our offices to incorporate LED lights, Energy Star appliances, and low flow plumbing fixtures.
C&C utilizes local suppliers and manufacturers whenever possible to not only reduce the carbon footprint of materials used on our projects, but to also support the local economies. A few examples are utilizing local Millwork Vendors, purchasing flooring from Floorfolio, who manufacturers their products in New Jersey, and working with lighting consultants to use light fixtures manufactured in New Jersey, Massachusetts, and other areas in the United States.
Design Development Phase
During this phase C&C will work with the project team to evaluate the project and produce design
development documents for pricing. We have assumed attendance at Bi-weekly or Monthly Design
Meetings with the project team to keep connected and abreast of any issues or design decisions. We will
schedule additional site visits to evaluate the existing conditions and perform exploratory work as required
to evaluate existing conditions and limit unforeseen challenges.
C&C will also review progress drawings for any constructability issues and or conflicts and hold separate
Design Coordination Meetings with selective subcontractors if needed. In addition we will use our in-house
Construction Review Document Checklist that we have developed through the years working on countless
senior living projects. C&C will collaborate with the Project Team to bring maximum value and efficiency to
the Frederick Living Phase 1 Project and specifically target the following areas.
Upon the completion of Design Development documents C&C will prepare the following:
• Itemized estimate based on typical unit/building layouts with selective subcontractor input
• Value Engineering Analysis and Recomendations
• Preliminary Project Schedules and Logistics Plans
Construction Documents Phase
As the drawings reach a more advanced stage C&C will assist the project team as needed and have assumed
continued attendance at Design Meetings. As more detailing is included in the drawings C&C will continue
to review the drawings for any additional constructability issues and provide feedback as necessary.
Upon completion of the construction documents C&C will prepare the following:
• Itemized GMP estimate with (3) subcontractor proposals for all trades
• Detailed Project Schedules
• Logistics Plans
CONSTRUCTION SERVICES
Agency Approvals
C&C will assist the owner and design professionals in obtaining all necessary agency approvals and permits.
We understand the importance of obtaining approvals to begin construction in a timely manner and
according to schedule. Our approach is to become familiar early on with the specific approvals in each
jurisdiction that we work and develop a working relationship with the individuals at each government
agency involved.
Job Meetings
Bi-weekly job meetings will be held with the project team to provide updates and look aheads as the project
progresses. Communication is the cornerstone of a successful project and C&C will establish a clear path of
communication and reporting for the project team. C & C will prepare meeting minutes and distribute to the
project team.
Toolbox talk meetings will also be held as necessary at the jobsite with subcontractors and onsite
management team. These meetings will be used to review construction activity coordination and will most
importantly reinforce safety procedures and specific concerns.